Liquid flow control devices serve several purposes in the flow industries. Some control the number of chemicals that get into the main liquid. Otters regulate the flow rate of fluids within a channel. Thus, there are several liquid-level control devices to serve various purposes.
Here, we will check all the types and their advantages. Stay tuned.
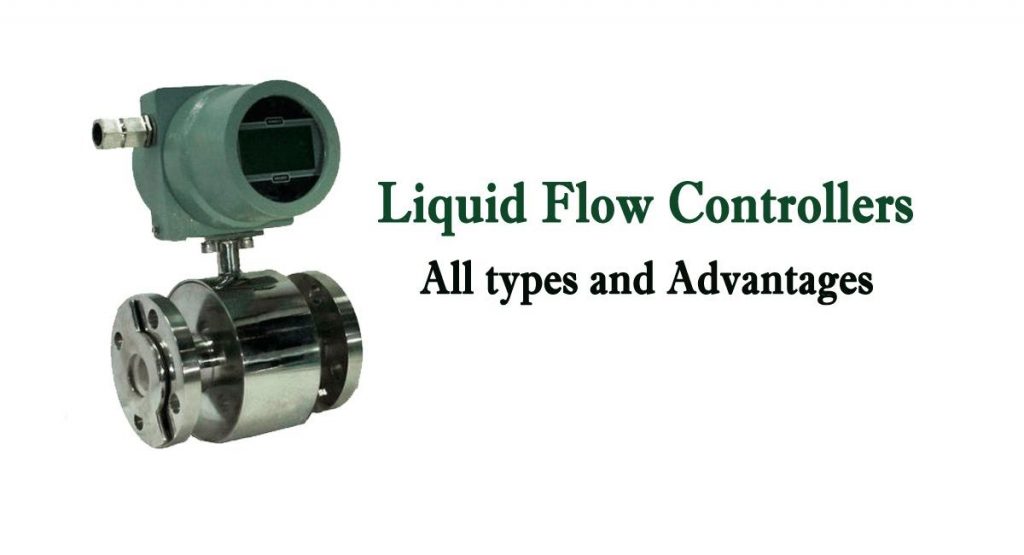
Gate Valves
Gate valves act as a gate to open and close a restriction on a flow channel. They work well on a straight channel. It will help if you use them where you don’t need flow restrictions.
You operate gate valves manually. Clockwise rotation closes the channel while anticlockwise will open the channel. If you rotate the gate valve halfway, you will restrict the flow or increase the pressure within the channel.
Globe Valves
They are linear motion valves that regulate, stop, or start the flow. You can use them for on/off and throttling applications. They are general-purpose liquid flow control valves useful in high heat applications.
Globe valves create a greater pressure drop than straight-through valves like gate valves. They have a closure that has a convex or flat bottom.
Pinch Valves
Slurry liquids and fluids with high amounts of suspended solids need a special kind of liquid flow control valve. Pinch valves are affordable and suitable for such types of applications. The valve uses a pinching effect to control the flow. Pinch valves have a 100% tight shut-off. You can use them in food processing, wastewater, chemical, and beverage firms.
Diaphragm Valves
Sometimes you may need a valve that is exclusively for throttling services. A diaphragm valve is your choice for use. You can use it with corrosive fluids at low pressure and temperature.
Diaphragm valves have a tight shut-off since they have a leak-proof seal. Also, you can easily clean and maintain the valve. You can repair the valve without interfering with the flow channel. However, you can only use the valve within a temperature range of -60? to 450? and a pressure not exceeding 300psi.
Check Valves
Check valves operate in one direction. They are useful in irrigation sprinklers, pumps, aircraft hydraulic systems, and other uses that need a unidirectional control valve. The valves have two ports- an inlet and an outlet. The valve doesn’t allow backflow. Thus your system compressor is safe from damage.
Needle Valves
Needle valves have features like those in globe valves. However, their uses are only in small lines- that’s why they have the name needle valves. Fluids flowing through this liquid flow control valve will turn 90 degrees then pass through an opening.
Just like the globe valve, a needle valve controls the flow through a rotating stem. However, a needle valve has higher precision than a globe valve.
Butterfly Valves
A butterfly valve doesn’t have linear flow traits. Thus, they have low precision to other valves. You should avoid them if flow restriction precision is important for your firm.
Butterfly valves are compact- it means they take up a little space. They are further classified with the position of the butterfly valve seat. Their main uses are in the labs, food, and beverage industries.
Ball Valves
They are also known as quarter-turn valves. They are helpful in industrial uses. You can use them to isolate or shut off the media.
Depending on the ball disc design, the ball valves can be floating or trunnion-mounted. Their body style helps in further classification of ball valves. The main classes are top entry, single body, and split body.
Non-Return Valves
These are valves that allow the fluid to flow in one direction only. One valve can fall into more than one category. For instance, check valves are an example of non-return valves. You install these valves where you suspect the flow condition may result in unwanted backflow.
Types of non-return valves include clapper type, spring-loaded type, and swing type. Their main aim is to prevent backflow to avoid contamination or damage to the flow system.
Pressure Release Valves
You can refer to these valves as safety relief valves. The valve’s functions are automatic. You set the valve to open when the pressure exceeds a certain level. The valve will help the excess pressure to escape, leaving the flow channel within the required pressure. Direct-acting spring valves and direct-acting dead-weight pressure valves are the two types of pressure release valves.
Solenoid Valves
These valves work with the help of an electromagnetic actuator. They are useful in pneumatic and hydraulic systems. The valves are either normally open or normally closed. Meaning, the valves remain open until you need to close or remain closed until you need to open.
Advantages of Liquid Flow Controllers
One of the greatest benefits of liquid level control valves is that most of them trigger action automatically. If your valve needs a manual operation, then you can change the flow any time you need.
Flow control valves compensate for the pressure changes within the flow system. That compensation ensures the flow conditions are stable.
All the control valves have reliable accuracy and repeatability. That’s why even the valves considered having lower precision find their way to medical fields.
Conclusion
Liquid flow control devices are useful in many situations. They help to keep the flow rate stable. Also, they are great for chemical injection in firms that need to add chemicals to the final product.
Author Bio :
Naman Modi is a Professional Blogger, SEO Expert & Guest blogger at proteusind.com, He is an Award-Winning Freelancer & Web Entrepreneur helping new entrepreneur?s launches their first successful online business.

As the editor of the blog, She curate insightful content that sparks curiosity and fosters learning. With a passion for storytelling and a keen eye for detail, she strive to bring diverse perspectives and engaging narratives to readers, ensuring every piece informs, inspires, and enriches.